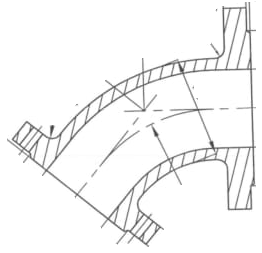
Knee pipe vacuum ladles are specialized components used in metal handling and pouring applications, requiring precision, durability, and resistance to high temperatures. Precision casting, or investment casting, is ideal for producing these complex parts. Here’s a concise guide to the process:
- Design: Create a detailed 3D CAD model, optimizing for casting with proper draft angles and allowances.
- Material Selection: Choose high-temperature-resistant alloys like stainless steel or heat-treated carbon steel.
- Pattern Creation: Fabricate a wax or 3D-printed pattern of the knee pipe and assemble it into a cluster.
- Mold Preparation: Build a ceramic shell around the pattern, then melt out the wax to form a hollow mold.
- Casting: Pour molten alloy into the preheated mold, ensuring it fills all intricate details.
- Post-Casting: Remove the ceramic shell, separate the castings, and clean and finish the surfaces.
- Inspection: Use non-destructive testing to ensure the ladle is defect-free.
- Machining: Perform precision machining on critical areas like joints and sealing surfaces.
Precision casting ensures knee pipe vacuum ladles meet high-performance standards, making them reliable for demanding industrial applications.